
EtO-Abatement-Plant
Sterilisation of medical devices with a touch of excellence
The complete safe solution for all ethylene oxide process emissions. LESNI's innovative and proven solution purifies the emissions from the sterilisation of medical devices. This delivers a safe and reliable "state of the art" system that meets the current stringent regulation with high destruction efficiency.
The recognised LESNI balancer/abator system provides a very controlled approach to handling competently hazardeous ethylene oxide gas. This secures lowest discharge emissions (currently as low as 0.5 mg/Nm³ according to German 'TA-Luft'), as well as demanding new NESHAP final rule for "Ethylene Oxide Emissions Standards for Sterilization Facilities Residual Risk and Technology Review", published by EPA in April 2024, fulfilling up to 99.99% destruction reduction efficiency (DRE) and better.
The Catalytic Abatement Plant "EO CAP" is designed to treat all potential low fugitive air extracts from degassing and aeration, the vacuum pump high concentrate vents as well as the waste liquid seal from vacuum pumps.
LESNI also design and supply quality "stand-alone" or integrated Preconditioning and Postconditioning (Degassing) Cells for the sterilization process. Energy costs are substantially reduced by the incorporation of well sized recuperative heat recovery.
These products for the sterilization process with ethylene oxide are used as a precaution and to protect users, the neighborhood and the environment from harmful environmental effects from air pollution.
Preconditioning Cell
Preconditioning is a necessary step in the sterilization process, which prepares products / devices ahead of sterilization and save precious time inside the sterilizer, it enhances ethylene oxide penetration into the product and packaging.
In the LESNI Preconditioning Cell, the products are in a temperature- and humidity-controlled area.
A typical range for this preconditioning step is a temperature of 40–60 °C and a relative humidity of 50–65%.
Product on pallets placed in a closed, insulated chamber where air flow, temperature, and relative humidity are evenly distributed and maintained at pre-set values.
Degassing Cell
Degassing is the next step after sterilization to get residual ethylene oxide out of the packaging and products by aerating the cell with heated air.
In the LESNI Degassing Cell, the products are in a temperature-controlled environment designed to ensure turbulent but accelerated air speed around the product to improve gas evaporation and reduce the degassing time.
A typical operating range for this degassing step is a temperature of 40–55 °C and several air changes.
Aeration time may vary and is related to product type and different materials used. For this reason, it is very important to have an efficient degassing and aeration stage to remove remaining ethylene oxide.
Vacuum Degassing Cell
Similar to standard Degassing Cell, a minimum air circulation rate will be targeted to achieve necessary turbulence throughout the cell. Also, the air flow will be distributed and balanced along the full length of the cell to give an even distribution of cell temperature and air flow conditions throughout the load. The inlet and outlet ducting will be designed to give the best atmosphere flow across the surface of all the product within the cell.
When loaded with sterilized product the cell door will be closed and sealed, with turbulent air circulated evenly around the product to give a homogenous atmosphere mix. This circulated atmosphere will then be heated to the cycle selected temperature point and maintained. Shallow vacuum intervals varying between 50 mbar and 700 mbar will follow at defined period to suit individual medical device product. Hold period of vacuum is attained and then atmospheric air break is performed. These vacuum/air breaks will continuously be performed for the selected duration of the degassing cycle phase in line with cycle recipe selected parameters.
The rapid degassing of EtO under slight shallow vacuum expected to reduce time of degassing by 65 % or more depending on the vacuum break performed.
Air Purification
Air Purification is the final step in the sterilization process, and without a doubt it’s the most important step, due to the potential risk associated with flammability and toxic nature of the ethylene oxide. LESNI solution focuses on the safety, performance, and reliability of the purification system to handle variable and peak concentrations of ethylene oxide from the process various stages.
The LESNI Catalytic Abatement Plant for ethylene oxide (EO CAP) is installed to purify exhaust air from production facilities or processes contaminated with organic compounds, which does not contain any components that can poison the catalyst. The organic pollutants are converted into CO2 and H2O on condition that all pollutants are compounds containing only carbon, hydrogen, nitrogen and oxygen.
The plant supersedes US emission limit legislations demanding new NESHAP final rule for "Ethylene Oxide Emissions Standards for Sterilization Facilities Residual Risk and Technology Review", published by EPA in April 2024, as well as meeting current European standards of less than 0.5 mg/Nm³ all the time (acc. to German legislation TA-Luft).
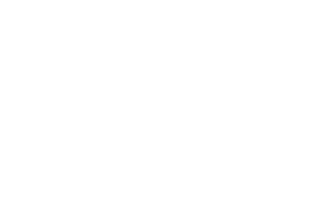